Hyundai Santa Fe: Cylinder Head Assembly / Cylinder Head. Repair procedures
•
|
Be careful not to damage the parts located under the vehicle
(floor under cover, fuel filter, fuel tank and canister) when
raising the vehicle using the lift.
(Refer to General Information - "Lift and Support Points")
|
|
•
|
Use fender covers to avoid damaging painted surfaces.
|
•
|
To avoid damaging the cylinder head, wait until the engine coolant
temperature drops below normal temperature before removing it.
|
•
|
When handling a metal gasket, take care not to fold the gasket
or damage the contact surface of the gasket.
|
•
|
To avoid damage, unplug the wiring connectors carefully while
holding the connector portion.
|
|
•
|
Mark all wiring and hoses to avoid misconnection.
|
|
1. |
Disconnect the battery negative terminal.
|
2. |
Remove the engine cover.
(Refer to Engine and Transaxle Assembly - "Engine Cover")
|
3. |
Remove the engine room under cover.
(Refer to Engine and Transaxle Assembly - "Engine Room Under Cover")
|
4. |
Drain the coolant.
(Refer to Cooling System - "Coolant")
|
5. |
Drain the engine oil.
(Refer to Lubrication System - "Engine Oil")
|
6. |
Remove the air duct and air cleaner assembly.
(Refer to Intake and Exhaust System - "Air Cleaner")
|
7. |
Remove the battery tray.
(Refer to Engine Electrical System - "Battery")
|
8. |
Disconnect the radiator upper hose (A).
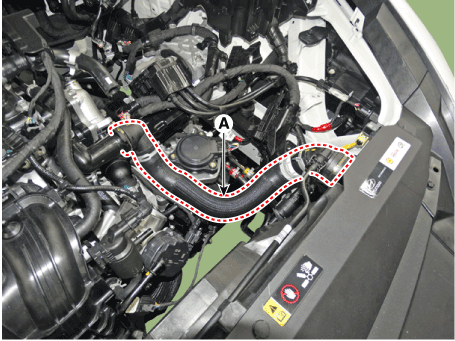
|
9. |
Disconnect the brake vacuum hose (A).
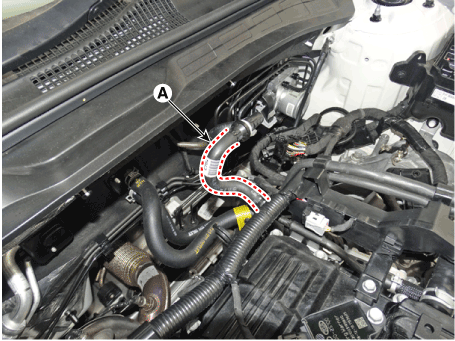
|
10. |
Disconnect the fuel hose (A) and purge control solenoid valve (PCSV)
hose (B).
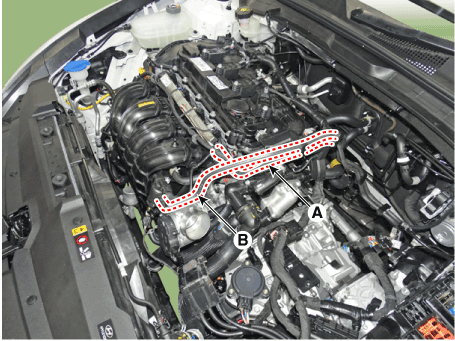
|
11. |
Remove the delivery pipe.
(Refer to Engine Control / Fuel System - "Delivery Pipe")
|
12. |
Remove the intake manifold.
(Refer to Intake and Exhaust System - "Intake Manifold")
|
13. |
Remove the exhaust manifold.
(Refer to Intake and Exhaust System - "Exhaust Manifold")
|
14. |
Remove the water temperature control assembly.
(Refer to Cooling System - "Water Temperature Control Assembly")
|
15. |
Remove the timing chain.
(Refer to Timing System - "Timing Chain")
|
16. |
Remove the camshaft front bearing cap (A) and camshaft bearing caps
(B).
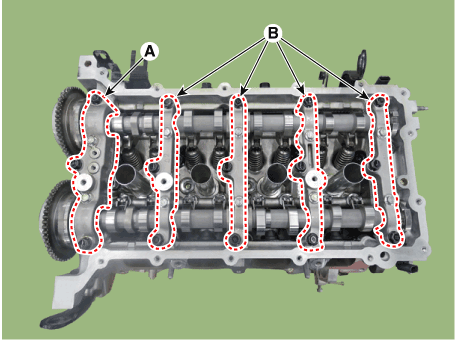
|
17. |
Remove the intake camshaft & CVVT assembly (A).
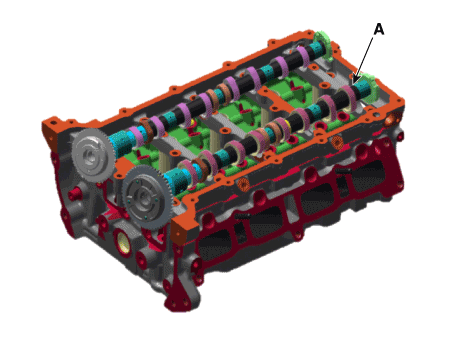
|
18. |
Remove the exhaust camshaft & CVVT assembly (A).
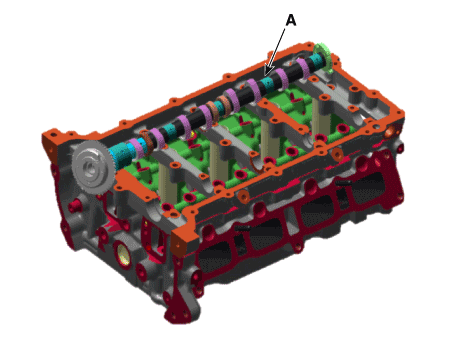
|
19. |
Remove the cam carrier (A).
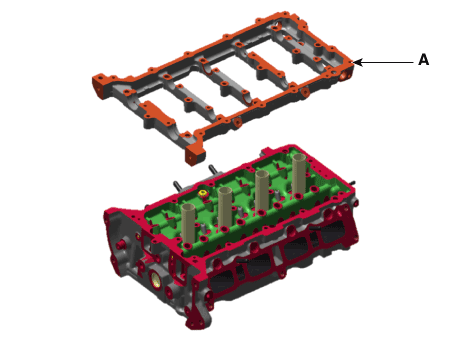
|
20. |
Remove the hydraulic lash adjuster (HLA) (A) and swing arm (B).
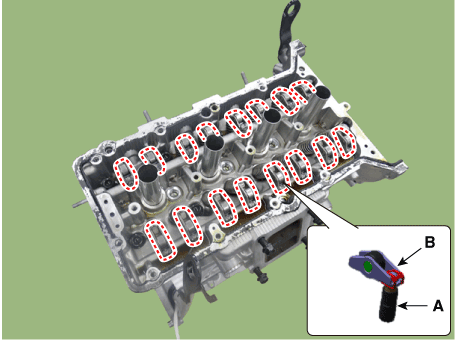
|
21. |
Remove the spark plug.
(Refer to Engine Electrical System - "Spark Plug")
|
22. |
Remove the cylinder head.
(1) |
Uniformly loosen and remove the cylinder head bolts, in several
passes, in the sequence shown.
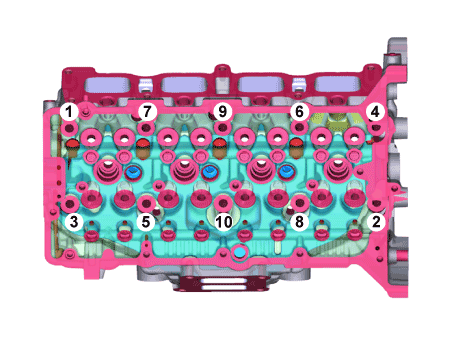
• |
Head warpage or cracking could result from removing
bolts in an incorrect order.
|
|
|
(2) |
Lift the cylinder head (A) from the dowels on the cylinder block
and place the cylinder head on wooden blocks on a bench.
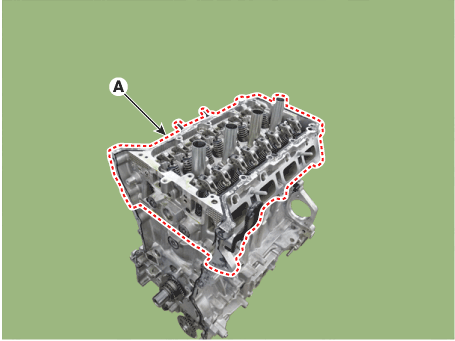
• |
Be careful not to damage the contact surfaces
of the cylinder head and cylinder block.
|
|
|
(3) |
Remove the cylinder head gasket (A).
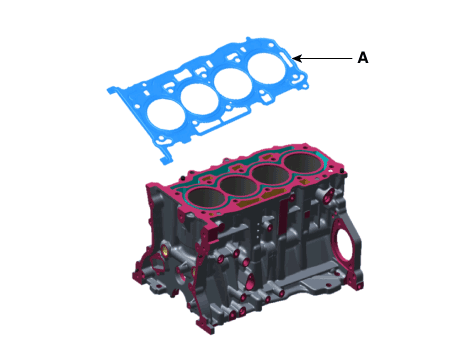
• |
Do not reuse the cylinder head gasket.
|
|
|
|
1. |
Remove the valves.
(1) |
Using SST (09222-3K000, 09222-3K100), compress the valve spring
and remove retainer lock.
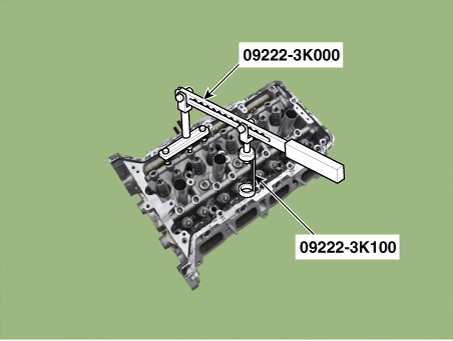
|
(2) |
Remove the spring retainer.
|
(3) |
Remove the valve spring.
|
(5) |
Using needle-nose pliers, remove the valve stem seal.
• |
Do not reuse old valve stem seals.
|
|
|
|
Cylinder Head
1. |
Inspect for flatness.
Using a precision straight edge and feeler gauge, measure the surface
the contacting the cylinder block and the manifolds for warpage.
Flatness of cylinder head gasket surface
Standard : Less than 0.05 mm (0.0019 in.) for total area
Less than 0.02 mm (0.0007 in.) for a section of 100 mm (3.9370
in.) X 100 mm (3.9370 in.)
Flatness of manifold mounting surface (Intake/Exhaust)
Standard : Less than 0.10 mm (0.0039 in.)
|
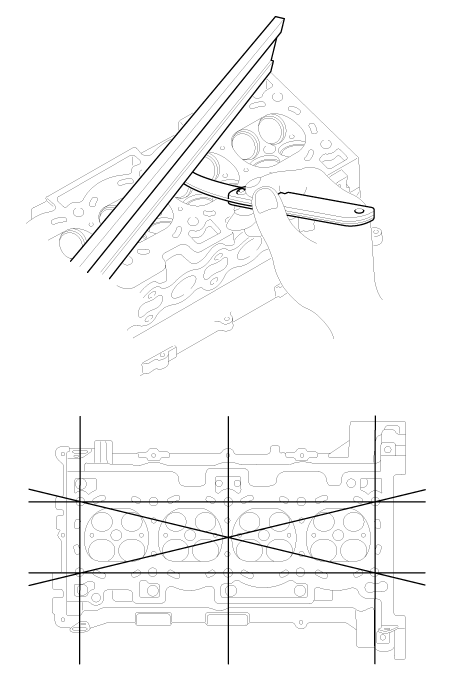
|
2. |
Inspect for cracks.
Check the combustion chamber, intake ports, exhaust ports and cylinder
block surface for cracks. If cracked, replace the cylinder head.
|
Valve And Valve Spring
1. |
Inspect valve stems and valve guides.
(1) |
Using a caliper gauge, measure the inside diameter of the valve
guide.
Valve guide inner diameter
Intake / Exhaust :
5.500 - 5.512 mm (0.21654 - 0.21701 in.)
|
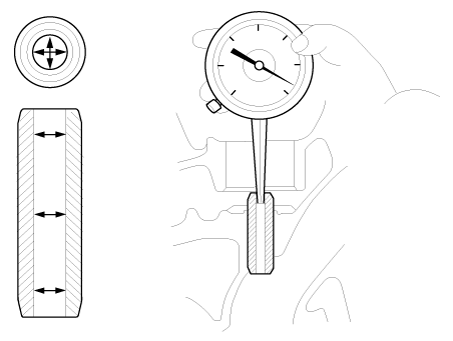
|
(2) |
Using a micrometer, measure the diameter of the valve stem.
Valve stem outer diameter
Intake : 5.460 - 5.475 mm (0.2150 - 0.2156 in.)
Exhaust : 5.453 - 5.465 mm (0.2147 - 0.2152 in.)
|
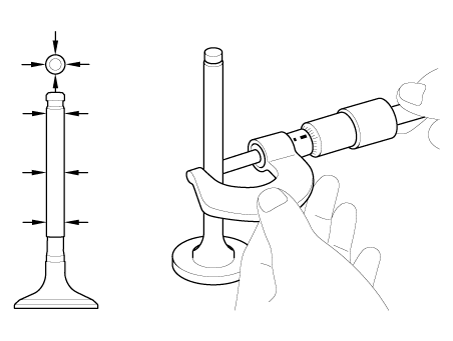
|
(3) |
Subtract the valve stem diameter measurement from the valve
guide inside diameter measurement.
Valve stem-to-guide clearance
[Standard]
Intake : 0.020 - 0.047 mm (0.00078 - 0.00185 in.)
Exhaust : 0.030 - 0.054 mm (0.00118 - 0.00212 in.)
[Limit]
Intake : 0.070 mm (0.00275 in.)
Exhaust : 0.090 mm (0.00354 in.)
|
If the clearance is greater than maximum, replace the valve
or cylinder head.
|
|
2. |
Inspect the valves.
(1) |
Check the valve is ground to the correct valve face angle.
|
(2) |
Check that the surface of the valve for wear.
If the valve face is worn, replace the valve.
|
(3) |
Check the valve head margin thickness.
Valve head thickness (Margin)
[Standard]
Intake : 0.8 mm (0.03150 in.)
Exhaust : 0.8 mm (0.03150 in.)
|
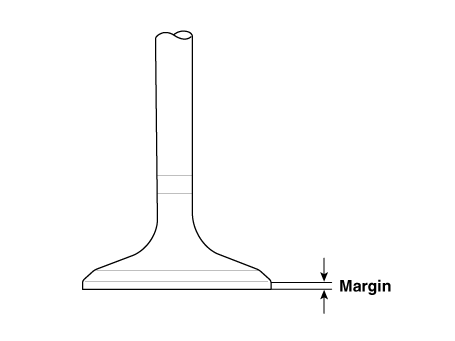
If the margin thickness is less than minimum, replace the valve.
|
(4) |
Check the valve length.
Valve length
[Standard]
Intake : 108.378 mm (4.2669 in.)
Exhaust :119.878 mm (4.7196 in.)
[Limit]
Intake : 108.228 mm (4.2609 in.)
Exhaust : 119.728 mm (4.7137 in.)
|
|
(5) |
Check the surface of the valve stem tip for wear.
If the valve stem tip is worn, replace the valve.
|
|
3. |
Inspect the valve seats
(1) |
Check the valve seat for evidence of overheating and improper
contact with the valve face. Replace the cylinder head if necessary.
|
(2) |
Check the valve guide for wear. If the valve guide is worn,
replace the cylinder head.
|
|
4. |
Inspect the valve springs.
(1) |
Using a steel square, measure the out-of-square of the valve
spring.
|
(2) |
Using a vernier calipers, measure the free length of the valve
spring.
Valve spring
[Standard]
Free height : 52.51 mm (2.0673 in.)
Out-of-square : Less than 1.5°
|
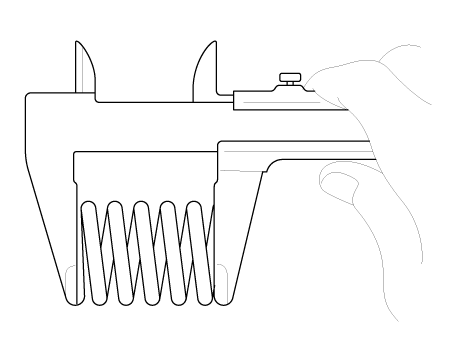
If the free length is not as specified, replace the valve spring.
|
|
•
|
Thoroughly clean all parts to be assembled.
Before installing the parts, apply fresh engine oil to all sliding
and rotating surfaces.
Replace oil seals with new ones.
|
|
1. |
Install valves.
(1) |
After applying engine oil to the valve stem seal, install a
new valve stem seal using the special tool (09222-2B100).
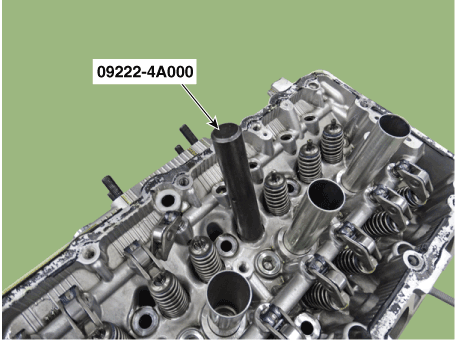
• |
Always use new valve stem seals.
|
• |
Incorrect installation of the seal could result
in oil leakage past the valve guides.
|
|
|
(2) |
Install the valve, valve spring and spring retainer.
• |
Place valve springs so that the side coated
with enamel faces toward the valve spring retainer
and then installs the retainer.
|
|
|
(3) |
Using the SST (09222-3K000, 09222-3K100), compress the spring
and install the retainer locks. After installing the valves,
ensure that the retainer locks are correctly in place before
releasing the valve spring compressor.
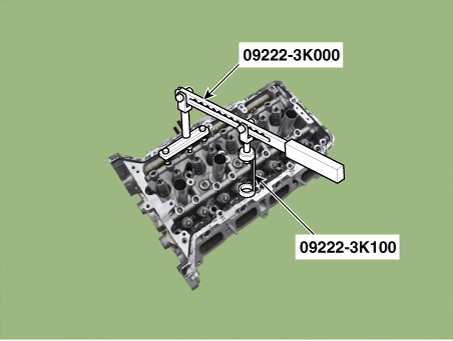
|
(4) |
Lightly tap the end of each valve stem two or three times with
the wooden handle of a hammer to ensure proper seating of the
valve and retainer lock.
|
|
2. |
Install the MLAs after appling engine oil.
|
•
|
Thoroughly clean all parts to be assembled.
|
•
|
Always use a new cylinder head gasket and manifold gasket.
|
•
|
Always use a new cylinder head bolt and cylinder head bolt washer.
|
•
|
The cylinder head and exhaust manifold is a metal gasket. Take
care not to bend it.
|
•
|
Turn the crankshaft pulley so that the No. 1 piston is at top
dead center.
|
|
1. |
Install the cylinder head.
(1) |
Remove hardening sealant, oil, dust, moisture and harmful foreign
materials from the cylinder block and the cylinder head.
|
(2) |
Apply liquid sealant on the upper surface of the cylinder block.
Width : 2.0 - 3.0 mm (0.0787 - 0.1181 in.)
Specification : MS721-40 TYPE "AA" or "AAO"
|
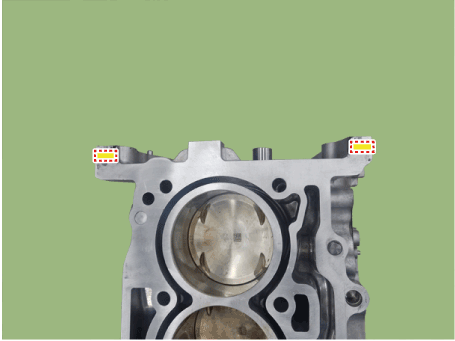
|
(3) |
Install the cylinder head gasket (A) to the cylinder block.
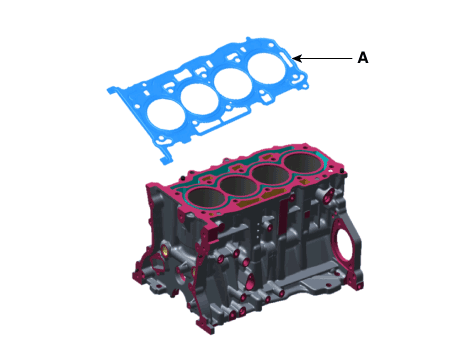
• |
Be careful of the installation direction.
|
|
|
(4) |
Apply liquid sealant on the upper surface of the cylinder head
gasket.
Width : 2.0 - 3.0 mm (0.0787 - 0.1181 in.)
Specification : MS721-40 TYPE "AA" or "AAO"
|
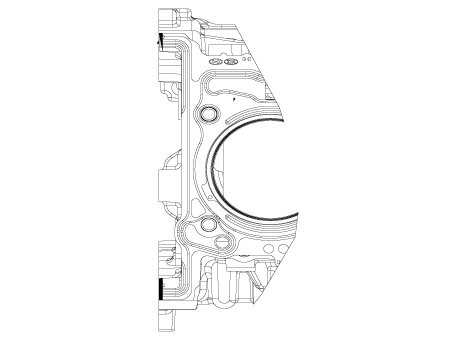
|
|
2. |
Install the cylinder head assembly.
(1) |
Place the cylinder head assembly (A) quietly in order not to
damage the gasket with the bottom part of the end.
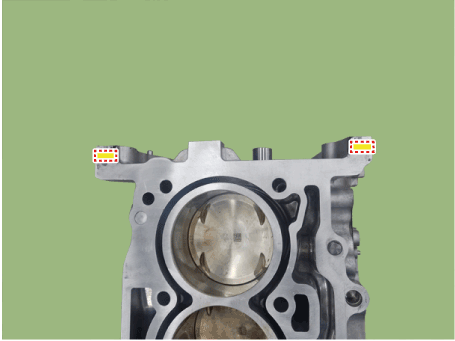
|
(2) |
Using SST (09221-4A000), tighten the cylinder head bolts and
plate washers, in several passes, in the sequence shown.
Tightening torque :
32.4 - 36.3 N.m (3.3 - 3.7 kgf.m, 23.9 - 26.8 lb-ft)
+ [90° - 94°] + [110° - 114°]
|
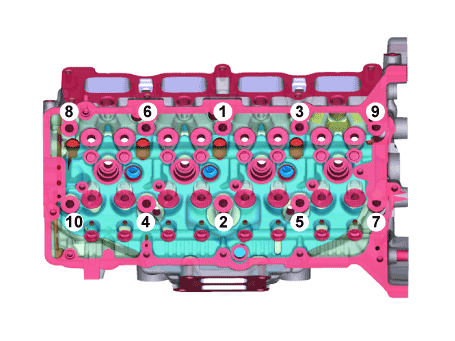
• |
Do not reuse the cylinder head bolts.
|
• |
Do not apply engine oil on the bolt threads
to achieve correct torque.
|
• |
Remove the extruded sealant within 5 minutes
after installing cylinder head bolts.
|
• |
The engine running or pressure test should not
be performed within 30minutes after installing
cylinder head bolts.
|
• |
Be careful not to change the installing position
of the preassembled washer bolts and non-preassembled
washer bolts.
|
|
|
|
3. |
Install the spark plugs.
(Refer to Engine Electrical System - "Spark Plug")
|
4. |
Install the hydraulic lash adjuster (HLA) (A) and the swing arm (B).
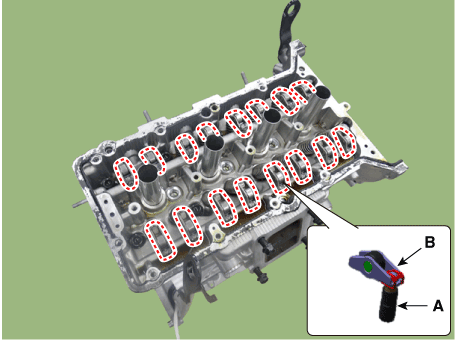
|
5. |
Install the cam carrier to the cylinder head.
(1) |
Remove hardening sealant, oil, dust, moisture and harmful foreign
materials from the bottom surface of the cam carrier and top
surface of the cylinder head.
|
(2) |
After applying liquid sealant on the bottom surface of the cam
carrier, Continuous bead of sealant should be applied to prevent
any path from oil leakage.
Width : 2.0 - 3.0 mm (0.0787 - 0.1181 in.)
Specification : MS721-40 TYPE "AA" or "AAO"
|
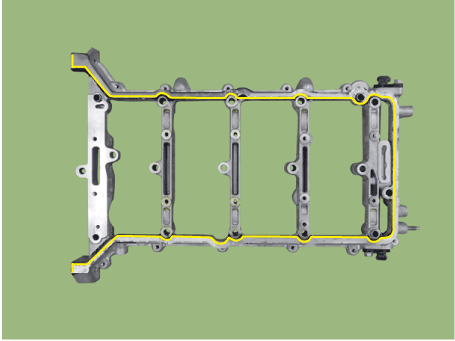
• |
When installing the cam carrier to the cylinder
head, make sure to prevent the sealant from
entering the hole (A) and the positive crankcase
ventilation (PCV).
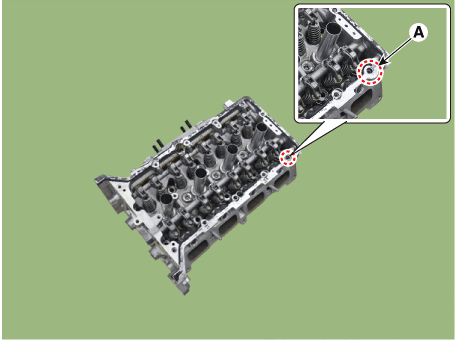
|
|
|
|
6. |
Install the cam carrier (A).
Tightening torque :
18.6 - 22.6 N.m (1.9 - 2.3 kgf.m, 13.7 - 16.6 lb-ft)
|
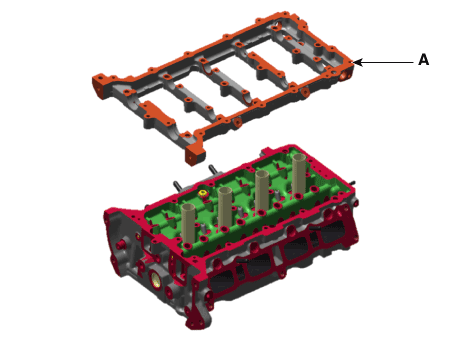
• |
Assemble the cam carrier within 5 minutes after applying
sealant.
|
• |
Assemble the camshaft bearing cap within 5 minutes after
assembling the cam carrier.
|
• |
The engine running or pressure test should not be performed
within 30 minutes after assembling the cam carrier.
|
• |
After installing the cam carrier to the cylinder head,
check whether there are sealants in the hole of the
oil level gauge and the positive crankcase ventilation
(PCV).
|
|
|
7. |
Install the intake CVVT & camshaft assembly (A).
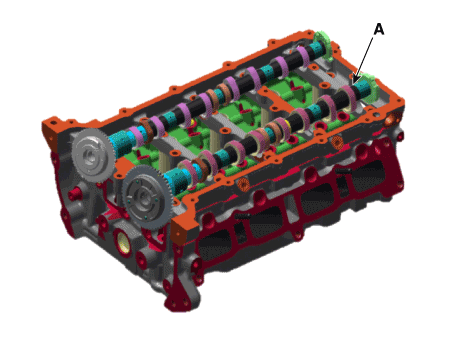
|
8. |
Install the exhaust CVVT & camshaft assembly (A).
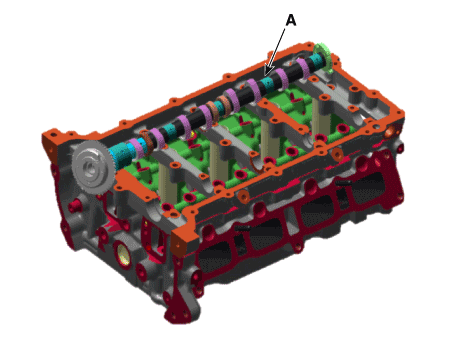
|
9. |
Install the camshaft front bearing cap (A) and camshaft bearing caps
(B).
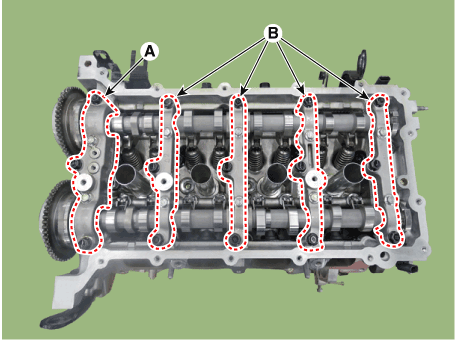
• |
When installing the camshaft front bearing cap and camshaft
bearing caps, tighten the bolts and nuts with pre-torque
first, and then tighten the bolts and nuts with specified
torque in the sequence shown.
Tightening torque :
Step 1
M8 Bolts : 9.8 - 11.8 N.m (1.0 - 1.2 kgf.m,
7.2 - 8.7 lb-ft)
M6 Bolts : 4.9 - 7.8 N.m (0.5 - 0.8 kgf.m, 3.6
- 5.8 Ib-ft)
Step 2
M8 Bolts : 18.6 - 22.6 N.m (1.9 - 2.3 kgf.m,
13.7 - 16.6 lb-ft)
M6 Bolts : 11.8 - 13.7 N.m (1.2 - 1.4 kgf.m,
8.7 - 10.1 lb-ft)
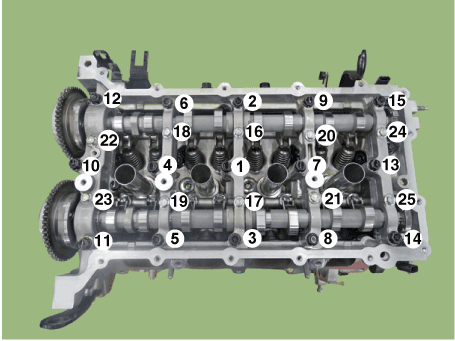
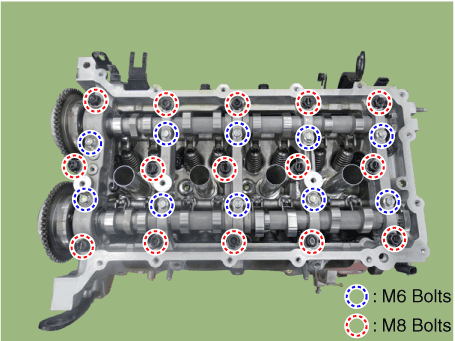
|
|
|
|
10. |
Install the other parts in the reverse order of removal.
|
11. |
Fill with engine coolant.
(Refer to Cooling System - "Coolant")
|
12. |
Refill engine with engine oil.
(Refer to Lubrication System - "Engine Oil")
|
Removal
•
Be careful not to damage the parts located under the vehicle
(floor under cover, fuel filter, fuel tank and canister) when
raising the vehicle using the lift...
Other information:
This function alerts driver when you get out of a car while the passengers remain
in the 2nd row seat.
If the front door is opened with passengers in the 2nd row seats, A warning message
will appear in the instrument cluster. After the 1st warning if movement is detected
in the 2nd row seat after all doors are locked, a second audible warning will be
triggered...
Removal
1.
Disconnect the negative (-) battery terminal.
2.
Remove the steering wheel.
(Refer to Steering System - "Steering Wheel")
3.
Remove the steering column upper and lower shrouds...
Categories
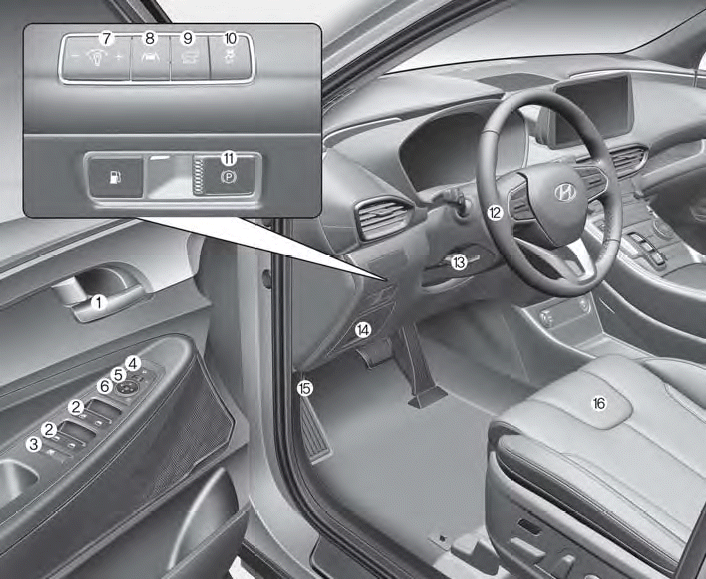
1. Inside door handle
2. Power window switches
3. Power window lock button/Electronic child safety lock button
4. Side view mirror folding button
5. Side view mirror control switch
6. Central door lock switch
7. Instrument panel illumination control switch
read more