Hyundai Santa Fe: Charging System / Battery. Repair procedures
Battery
1. |
Turn the ignition switch OFF and disconnect the battery (-) terminal
(A).
Tightening torque :
7.8 - 9.8 N.m (0.8 - 1.0 kgf.m, 5.8 - 7.2 Ib-ft)
|
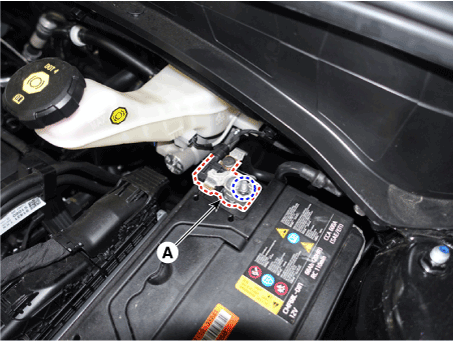
|
2. |
Disconnect the battery (+) terminal (A).
Tightening torque :
7.8 - 9.8 N.m (0.8 - 1.0 kgf.m, 5.8 - 7.2 Ib-ft)
|
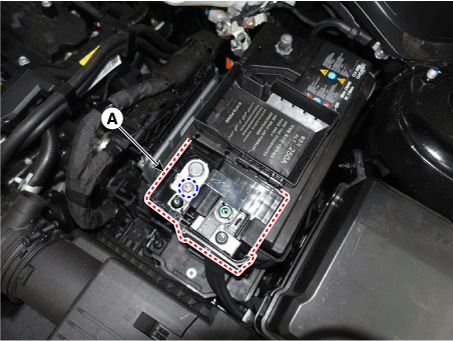
|
3. |
Remove the battery mouting bracket.
Tightening torque :
7.8 - 11.8 N.m (0.8 - 1.2 kgf.m, 5.8 - 8.7 Ib-ft)
|
|
4. |
Remove the battery (A).
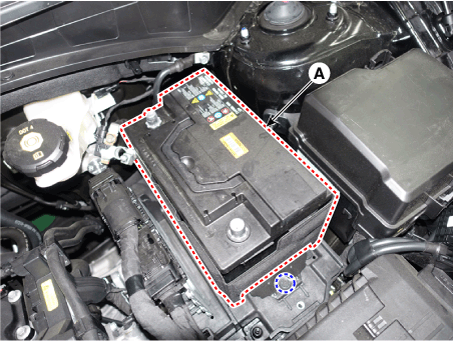
|
Battery Tray
2. |
Remove the air cleaner assembly.
(Refer to Engine Mechanical System - "Air Cleaner")
|
3. |
Remove the engine control module (ECM).
(Refer to Engine Control / Fuel System - "Engine Control Module (ECM)")
|
4. |
Remove the battery tray (A).
Tightening torque :
7.8 - 10.8 N.m (0.8 - 1.1 kgf.m, 5.8 - 8.0 Ib-ft)
|
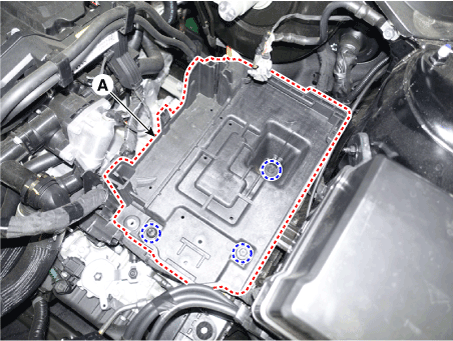
|
1. |
Install in the reverse order of removal.
• |
When installing the battery, fix the mounting bracket
on the tray correctly.
|
|
• |
After disconnecting then reconnecting the battery negative
cable, reset some parts that require the reset procedures.
(Refer to Body Electrical System - "General Information")
|
|
• |
ISG (Idle stop & go) system equipped vehicle always
use the AGM battery only. If flooded battery has installed,
this can potentially lead to engine electrical trouble
or ISG system error.
|
• |
Replace same capacity of the AGM battery.
|
|
• |
Do not open the AGM battery.
|
• |
The AGM battery must not be opened under any circumstances
as the introduction of oxygen from the air will cause
the battery to lose its chemical equilibrium and rendered
non-operational.
|
|
|
Battery Condition
Check the battery for damage or deformation. If severe damage, deformation or
leakage is found, replace the battery.
Vehicle parasitic current inspection
[Using the Ammeter]
1. |
Turn the all electric devices OFF, and then turn the ignition switch
OFF.
|
2. |
Close all doors except the engine hood, and then lock all doors.
(1) |
Disconnect the hood switch connector.
|
(3) |
Close the doors or remove the door switches.
|
|
3. |
Wait a few minutes until the vehicle’s electrical systems go to sleep
mode.
• |
For an accurate measurement of a vehicle parasitic current,
all electrical systems should go to sleep mode. (It
takes at least one hour or at most one day.) However,
an approximate vehicle parasitic current can be measured
after 10-20 minutes.
|
|
|
4. |
Connect an ammeter in series between the battery (-) terminal and the
ground cable, and then disconnect the clamp from the battery (-) terminal
slowly.
• |
Be careful that the lead wires of an ammeter do not
come off from the battery (-) terminal and the ground
cable to prevent the battery from being reset. In case
the battery is reset, connect the battery cable again,
and then start the engine or turn the ignition switch
ON for more than 10 sec. Repeat the procedure from No.
1.
To prevent the battery from being reset during the inspection,
|
1) |
Connect a jump cable between the battery (-) terminal
and the ground cable.
|
2) |
Disconnect the ground cable from the battery (-) terminal.
|
3) |
Connect an ammeter between the battery (-) terminal
and the ground cable.
|
4) |
After disconnecting the jump cable, read the current
value of the ammeter.
|
|
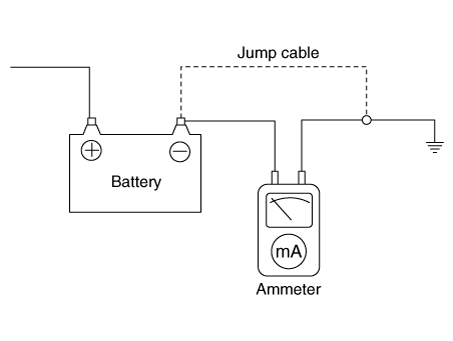
|
5. |
Read the current value of the ammeter.
•
|
If the parasitic current is over the limit value, search for
abnormal circuit by removing a fuse one by one and checking
the parasitic current.
|
•
|
Reconnect the suspected parasitic currentdraw circuit fuse only
and search for suspectedunit by removing the component connected
with thecircuit one by one until the parasitic draw dropsbelow
limit value.
|
Limit value (after 10 - 20 min.) : Below 50 mA
|
|
[Using the Clamp type Ammeter]
1. |
Turn the all electric devices OFF, and then turn the ignition switch
OFF.
|
2. |
Close all doors except the engine hood, and then lock all doors.
(1) |
Disconnect the hood switch connector.
|
(3) |
Close the doors or remove the door switches.
|
|
3. |
Wait a few minutes until the vehicle’s electrical systems go to sleep
mode.
• |
For an accurate measurement of a vehicle parasitic current,
all electrical systems should go to sleep mode. (It
takes at least one hour or at most one day.) However,
an approximate vehicle parasitic current can be measured
after 10-20 minutes.
|
|
|
4. |
Install the clamp type ammerter on battery negative (-) terminal.
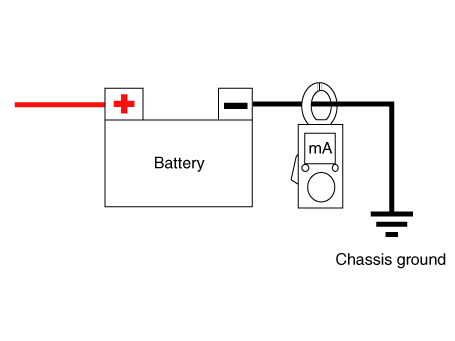
|
5. |
Read the current value of the ammeter.
•
|
If the parasitic current is over the limit value, search for
abnormal circuit by removing a fuse one by one and checking
the parasitic current.
|
•
|
Reconnect the suspected parasitic currentdraw circuit fuse only
and search for suspectedunit by removing the component connected
with thecircuit one by one until the parasitic draw dropsbelow
limit value.
|
Limit value (after 10 - 20 min.) : Below 50 mA
|
|
The Micro 570 Analyzer provides the ability to test the charging and starting
systems, including the battery, starter and alternator.
※ Because of the possibility of personal injury, always use extreme
caution and appropriate eye protection when working with batteries.
※ When charging battery by test result, Battery must be fully charged.
To get accurate test result, battery surface voltage must have subsided
ahead before test when you test battery after charged. (See following
Battery Test Results)
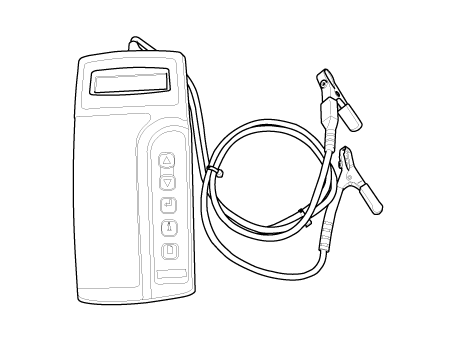
|
Keypad
The Micro 570 button on the key pad provide the following functions :
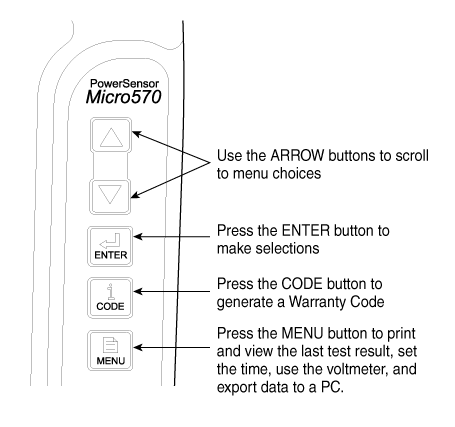
Battery Test Procedure
1. |
Connect the tester to the battery.
–
|
Red clamp to battery positive (+) terminal.
|
–
|
Black clamp to battery negative (-) terminal.
|
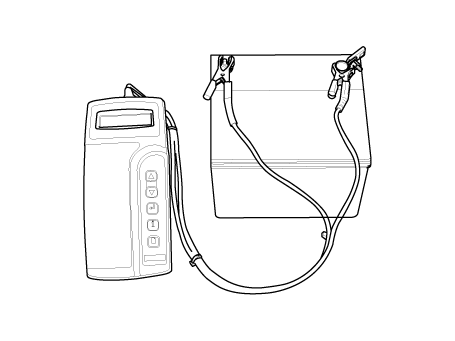
• |
Connect clamps securely. If "CHECK CONNECTION" message
is displayed on the screen, reconnect clamps securely.
|
|
|
2. |
The tester will ask if the battery is connected "IN-VEHICLE" or "OUT-OF-VEHICLE".
Make your selection by pressing the arrow buttons; then press ENTER.
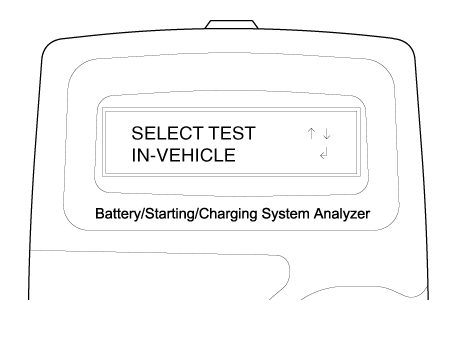
|
3. |
Select CCA and press the ENTER button.
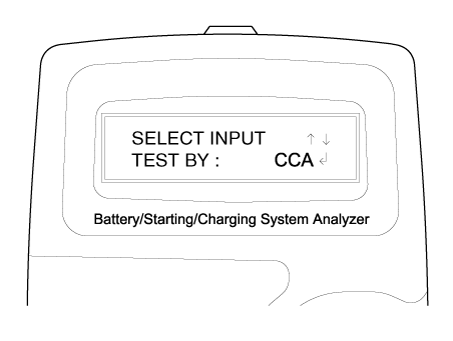
• |
CCA : Cold cranking amps, is an SAE specification for
cranking batteried at -0.4°F (-18°C).
|
|
|
4. |
Set the CCA value displayed on the screen to the CCA value marked on
the battery label by pressing up and down buttons and press ENTER.
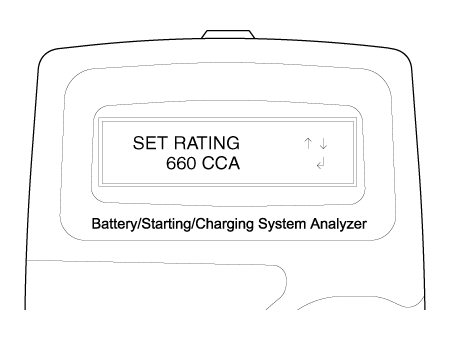
• |
The battery ratings (CCA) displayed on the tester must
be identical to the ratings marked on battery label.
|
|
|
5. |
The tester will conduct battery test.

|
6. |
The tester displays battery test results including voltage and battery
ratings.
Refer to the following table and take the appropriate action as recommended
by the Micro 570.
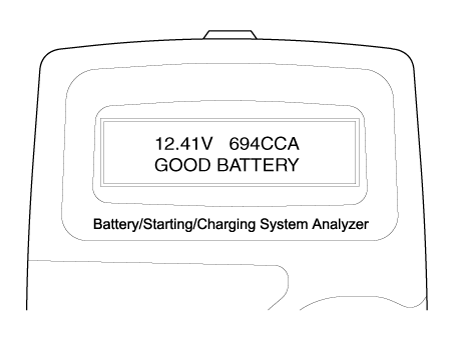
Battery Test Results
Result On Printer
|
Remedy
|
GOOD BATTERY
|
No action is required.
|
GOOD RECHARGE
|
Battery is in a good state.
Recharge the battery and use.
※ You have to follow instruction below when you charge battery and
retest, otherwise test result can be inaccurate. (See ‘Charge and
Retest method after battery charge’ below.)
|
CHARGE & RETEST
|
Battery is not charged properly.
– |
Charge and test the battery again.
|
※ You have to follow instruction below when you charge battery and
retest, otherwise test result can be inaccurate. (See ‘Charge and
Retest method after battery charge’ below.)
|
REPLACE BATTERY
|
Replace battery and recheck the charging system.
– |
Improper connection between battery and vehicle cables
may cause "REPLACE BATTERY". Retest the battery after
removing cables and connecting the tester to the battery
terminal directly prior to replacing the battery.
|
|
BAD CELL-REPLACE
|
Charge and retest the battery.
– |
If the Micro 570 recommends "REPLACE BATTERY", replace
the battery and recheck the charging system.
|
|
[Charge and Retest method after battery charge]
Battery charge
Set battery charger to ‘Auto Mode’ (The Mode that charging current drops
as the battery charges.) and charge battery until charging current down
close to zero or the charger alerts you with an alarm when charge is
complete.
(Minimum charging time recommended: More than 3 hours with Auto Mode
that explained above)
•
|
If battery is not fully charged, battery surface voltage will
be high while the amount of current charged (CCA) in battery
is low. If you measure the battery under this condition, tester
may misjudge that battery sulfation occurred because the amount
of current in battery is too low in comparison with battery
voltage.
* Surface voltage: When battery is charged electrolyte temperature
increases and chemical reaction become active resulting in an
excessive increase of battery voltage.
It is known that it takes approximate one day to subside this
increased surface voltage completely.
|
Battery Test after charge
Do not test battery right after the charge. Test battery after battery
surface voltage has subsided as instructed in the following procedure.
(1) |
When battery charge is complete, install the battery in the
vehicle.
|
(2) |
Put IG key to ON position and turn on head lamp with low beam,
and wait 5 minutes. (Discharge for 5 minutes)
|
(3) |
Turn off the head lamp and IG key, and wait 5 minutes. (Waiting
for 5 minutes)
|
(4) |
Remove +, - cable from the battery and test battery.
|
• |
Whenever filing a claim for battery, the print out of
the battery test results must be attached.
|
|
Starter Test Procedure
|
7. |
After the battery test, press ENTER immediately for the starter test.
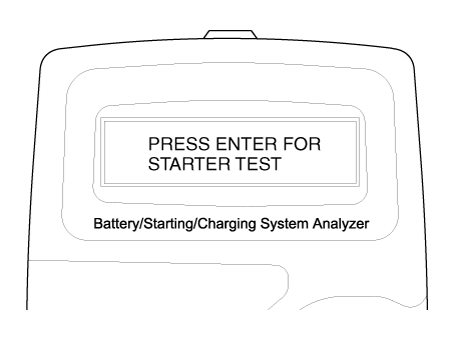
|
8. |
Start the engine.
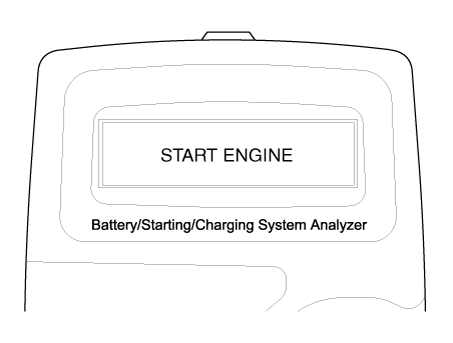
|
9. |
Cranking voltage and starter test results will be displayed on the screen.
Refer to the following table and take the appropriate action as recommended
by the Micro 570.
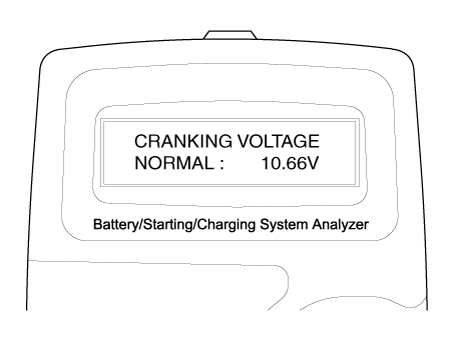
Starter Test Results
Result On Printer
|
Remedy
|
CRANKING VOLTAGE NORMAL
|
System shows a normal starter draw.
|
CRANKING VOLTAGE LOW
|
Cranking voltage is lower than normal level.
|
CHARGE BATTERY
|
The state of battery charge is too low to test.
– |
Charge the battery and retest.
|
|
REPLACE BATTERY
|
Replace battery.
– |
If the vehicle is not started though the battery condition
of "GOOD BATTERY" is displayed, check wiring for open
circuit, battery cable connection, starter and repair
or replace as necessary.
|
– |
If the engine does crank, check fuel system.
|
|
• |
When testing the vehicle with old diesel engines, the
test result will not be favorable if the glow plug is
not heated. Conduct the test after warming up the engine
for 5 minutes.
|
|
Charging System Test Procedure
|
10. |
Press ENTER to begin charging system test.
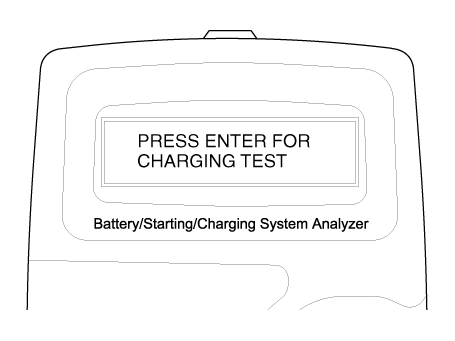
|
11. |
The tester displays the actual voltage of alternator.
Press ENTER to continue.
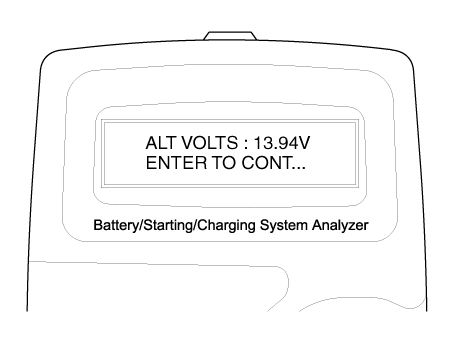
|
12. |
Turn off all electrical load and rev engine for 5 seconds with pressing
the accelerator pedal. (Follow the instructions on the screen)
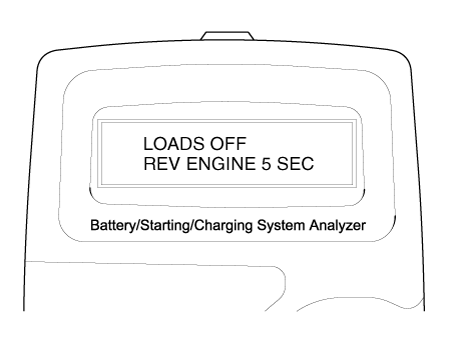
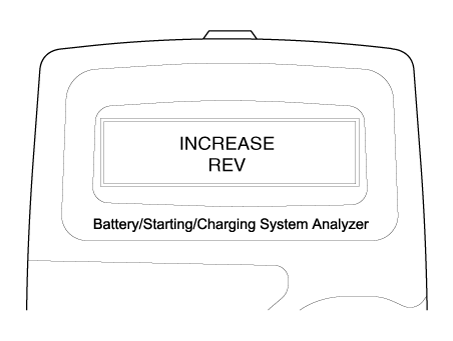
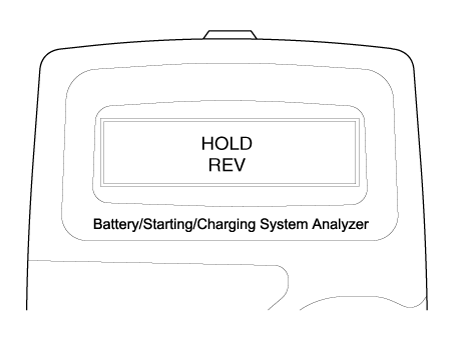
|
13. |
The message that engine RPM is detected will be displayed on the screen.
Press ENTER to continue.
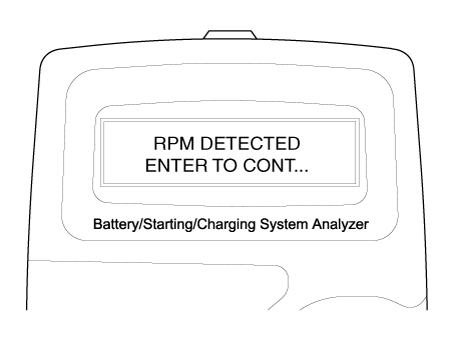
|
14. |
If the engine RPM is not detected, press ENTER after revving engine.
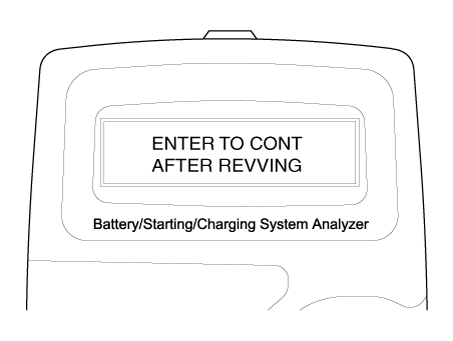
|
15. |
The tester will conduct charging system test during loads off.
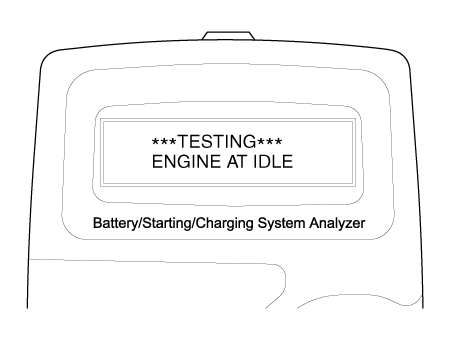
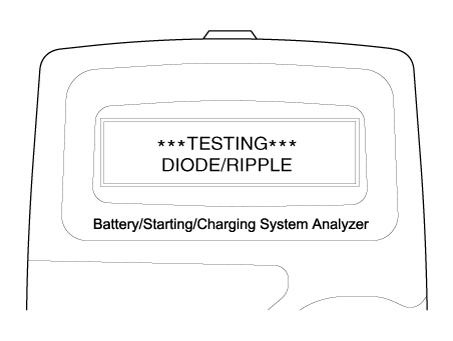
|
16. |
Turn on electrical loads (air conditioner, lamps, audio and etc). Press
ENTER to continue.
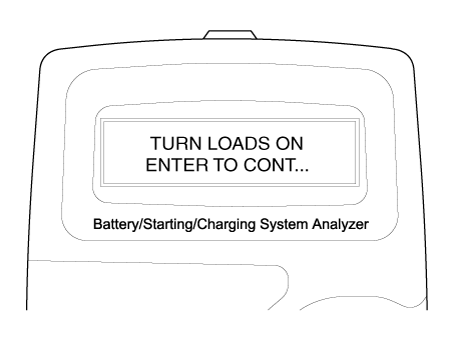
|
17. |
The tester will conduct charging system test during loads on.
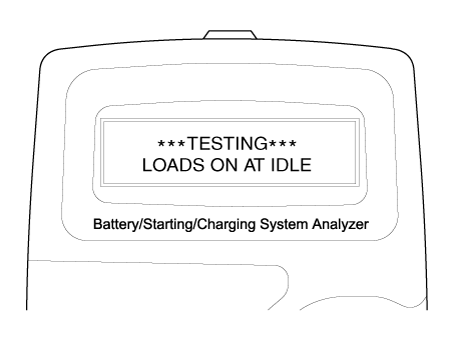
|
18. |
Rev engine for 5 seconds with pressing the accelerator pedal. (Follow
the instructions on the screen)
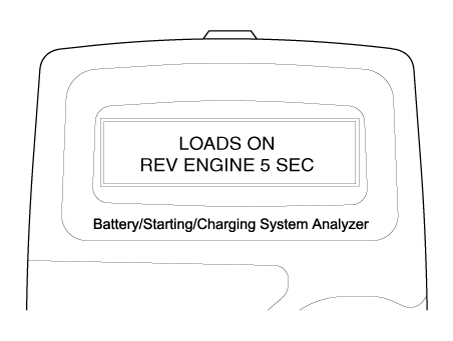
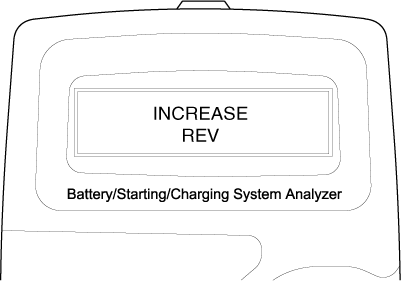
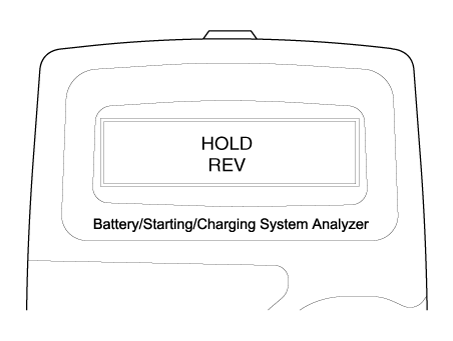
|
19. |
The message that engine RPM is detected will be displayed on the screen.
Press ENTER to continue.
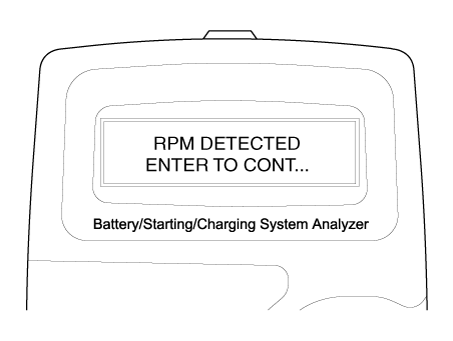
|
20. |
If the engine RPM is not detected, press ENTER after revving engine.
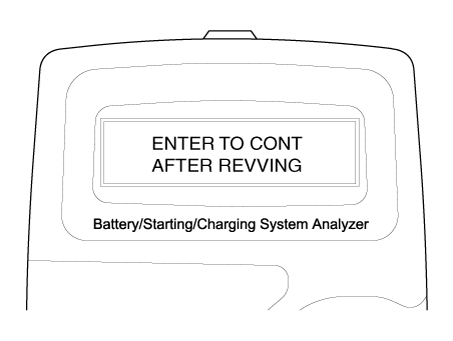
|
21. |
Turn off electrical loads (air conditioner, lamps, audio and etc). Turn
the engine off.
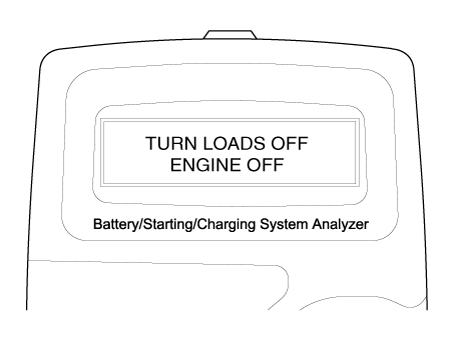
|
22. |
Charging voltage and charging system test results will be displayed
on the screen.
Shut off engine end disconnect the tester clamps from the battery. Refer
to the following table and take the appropriate action as recommended
by the Micro 570.
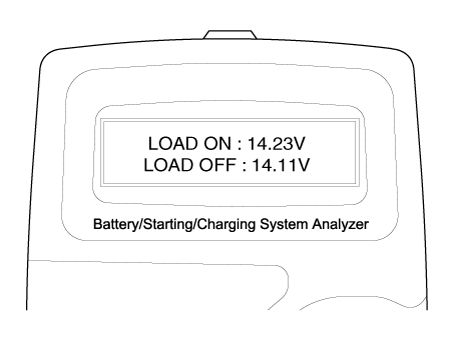
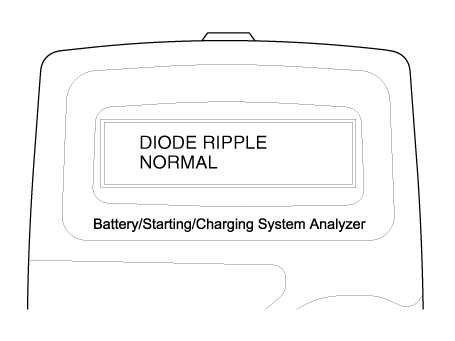
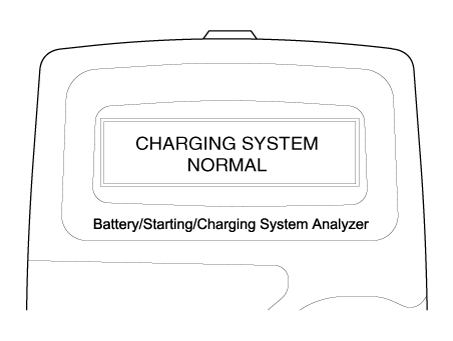
Charging System Test Results
Result On Printer
|
Remedy
|
CHARGING SYSTEM NORMAL / DIODE RIPPLE NORMAL
|
Charging system is normal.
|
NO CHARGING VOLTAGE
|
Alternator does not supply charging current to battery.
– |
Check belts, connection between alternator and battery
and replace belts or cable or alternator as necessary.
|
|
LOW CHARGING VOLTAGE
|
Alternator does not supply charging current to battery and electrical
load to system fully.
– |
Check belts and alternator and replace as necessary.
|
|
HIGH CHARGING VOLTAGE
|
The voltage from alternator to battery is higher than normal limit
during voltage regulating.
– |
Check connection and ground and replace regulator as
necessary.
|
– |
Check electrolyte level in the battery.
|
|
EXCESS RIPPLE DETECTED
|
One or more diodes in the alternator is not functioning properly.
– |
Check alternator mounting and belts and replace as necessary.
|
|
|
The MDX-670P Analyzer
The MDX-670P battery conductance and electrical system analyzer tests batteries
as well as starting and charging systems for vehicle.
It displays the test results in seconds and features a built-in printer to provide
a copy of the results.
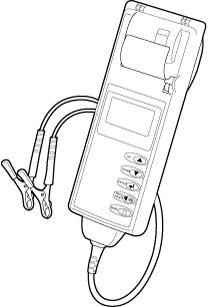
1) |
Because of the possibility of personal injury, always use extreme
caution and appropriate eye protection when working with batteries.
|
2) |
When charging battery by test result, Battery must be fully
charged. To get accurate test result, battery surface voltage
must have subsided ahead before test when you test battery after
charged. (See following Battery Test Results)
|
|
•
|
When testing the vehicle with old diesel engines, the test result
will not be favorable if the glow plug is not heated. Conduct
the test after warming up the engine for 5 minutes.
|
|
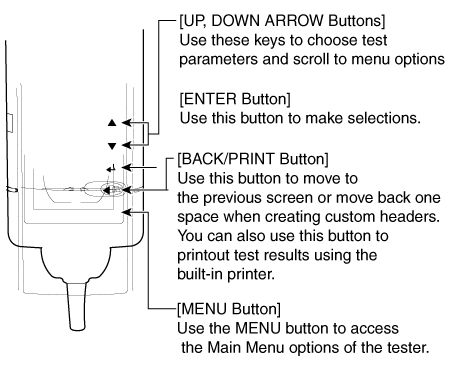
1. |
Connect the red clamp to the positive (+) terminal and the black clamp
to the negative (–) terminal.
• |
For a proper connection, rock the clamps back and forth.
The tester requires that both sides of each clamp be
firmly connected before testing. A poor connection will
produce a CHECK CONNECTION or WIGGLE CLAMPS message.
If the message appears, clean the terminals and reconnect
the clamps.
|
|
|
2. |
Scroll to and select IN VEHICLE or OUT OF VEHICLE for a battery not
connected to a vehicle.
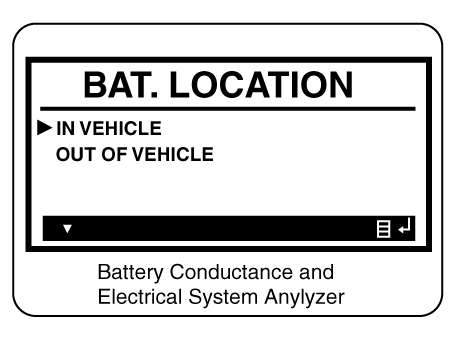
• |
Following an IN VEHICLE test you will be prompted to
test the starting and charging systems.
|
|
|
3. |
Scroll to and select REGULAR FLOODED, AGM FLAT PLATE, or AGM SPIRAL
where applicable.
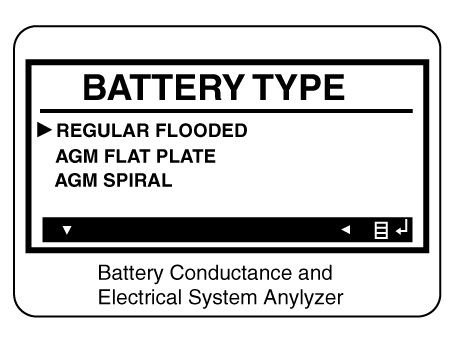
• |
If the vehicle equipped with ISG function, select the
AGM FLAT PLATE.
|
|
|
4. |
Scroll to and select the battery’s rating system.
• |
Mostly, the CCA value is marked on the battery label,
but sometimes marked EN or SEA value. Select one of
them.
|
|
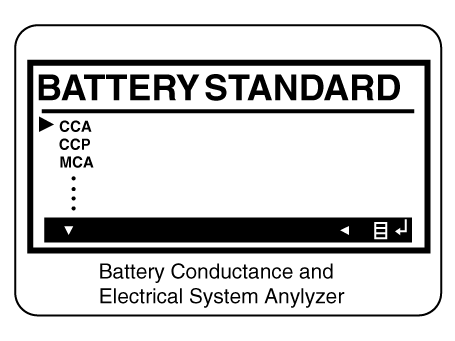
–
|
CCA : Cold Cranking Amps, as specified by SAE. The most common
rating for cranking batteries at 0°F (-17.8 °C).
|
–
|
SAE : Society of Automotive Engineers, the European labeling
of CCA
|
|
5. |
Set the selected rating value displayed on the screen to the value marked
on the battery label by pressing up and down arrow buttons.
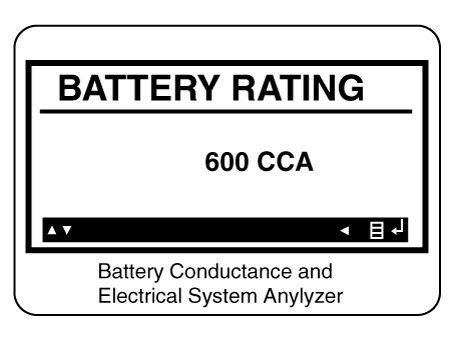
|
6. |
Press ENTER to start test.
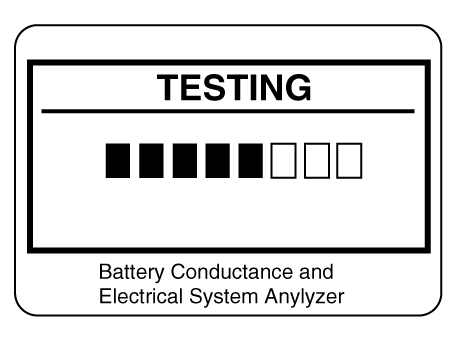
|
7. |
After several seconds the tester displays the decision on the battery’s
condition and the measured voltage. The tester also displays your selected
battery rating and the rating units.
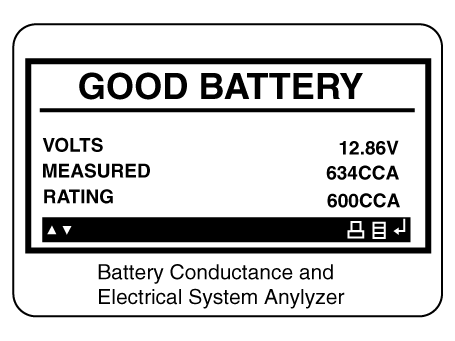
Battery Test Results
Result On Printer
|
Remedy
|
GOOD BATTERY
|
No action is required.
|
GOOD RECHARGE
|
Battery is in a good state. Recharge the battery and use.
※ You have to follow instruction below when you charge battery and
retest, otherwise test result can be inaccurate. (See ‘Charge and
Retest method after battery charge’ below.)
|
CHARGE & RETEST
|
Battery is not charged properly.
– |
Charge and test the battery again.
|
※ You have to follow instruction below when you charge battery and
retest, otherwise test result can be inaccurate. (See ‘Charge and
retest method after battery charge’ below.)
|
REPLACE BATTERY
|
Replace battery and recheck the charging system.
– |
Improper connection between battery and vehicle cables
may cause "REPLACE BATTERY", retest the battery after
removing cables and connecting the tester to the battery
terminal directly prior to replacing the battery.
|
|
BAD CELLREPLACE
|
Charge and retest the battery.
– |
If recommends "REPLACE BATTERY", replace the battery
and recheck the charging system.
|
|
[Charge and Retest method after battery charge]
Battery charge
Set battery charger to ‘Auto Mode’ (The Mode that charging current drops
as the battery charges.) and charge battery until charging current down
close to zero or the charger alerts you with an alarm when charge is
complete.(Minimum charging time recommended: More than 3 hours with
Auto Mode that explained above)
•
|
If battery is not fully charged, battery surface voltage will
be high while the amount of current charged (CCA) in battery
is low. If you measure the battery under this condition, tester
may misjudge that battery sulfation occurred because the amount
of current in battery is too low in comparison with battery
voltage.
* Surface voltage: When battery is charged electrolyte temperature
increases and chemical reaction become active resulting in an
excessive increase of battery voltage.
It is known that it takes approximate one day to subside this
increased surface voltage completely.
|
Battery Test after charge
Do not test battery right after the charge. Test battery after battery
surface voltage has subsided as instructed in the following procedure.
(1) |
When battery charge is complete, install the battery in the
vehicle.
|
(2) |
Put IG key to ON position and turn on head lamp with low beam,
and wait 5 minutes. (Discharge for 5 minutes)
|
(3) |
Turn off the head lamp and IG key, and wait 5 minutes. (Waiting
for 5 minutes)
|
(4) |
Remove +, - cable from the battery and test battery.
|
• |
For an in-vehicle test, the display alternates between
the test results and the message "PRESS FOR STARTER
TEST".
|
|
• |
Before starting the test, inspect the alternator drive
belt. A belt that is glazed or worn, or lacks the proper
tension, will prevent the en¬gine from achieving the
rpm levels needed for the test.
|
|
|
8. |
Press the ENTER button to proceed with the starter test.
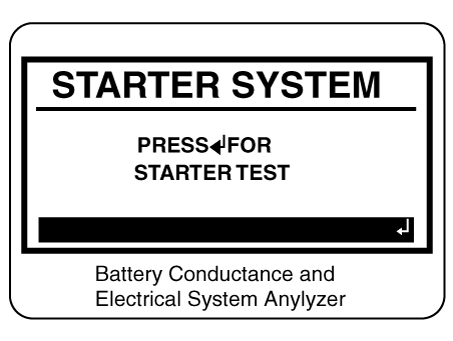
|
9. |
Start the engine when prompted.
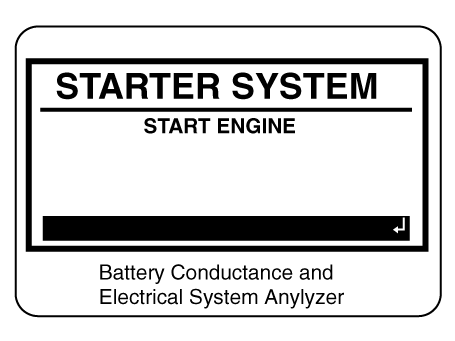
|
10. |
The tester displays the decision on the starter system, cranking voltage,
and cranking time in milliseconds.
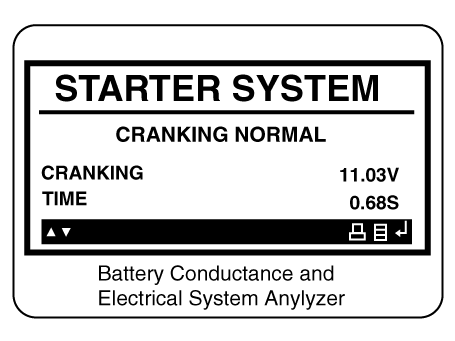
Starter Test Results
Result On Printer
|
Remedy
|
CRANKING VOLTAGE NORMAL
|
System shows a normal starter draw.
|
CRANKING VOLTAGE LOW
|
Cranking voltage is lower than normal level.
|
CHARGE BATTERY
|
The state of battery charge is too low to test.
– |
Charge the battery and retest.
|
|
REPLACE BATTERY
|
Replace battery.
– |
If the vehicle is not started though the battery condition
of "GOOD BATTERY" is displayed, check wiring for open
circuit, battery cable connection, starter and repair
or replace as necessary.
|
– |
If the engine does crank, check fuel system.
|
|
• |
For an in-vehicle test, the display alternates between
the test results and the message "PRESS FOR CHARGING
TEST.
|
|
Step 3 : Charging System Test
|
11. |
Press the ENTER button to proceed with the charging test.
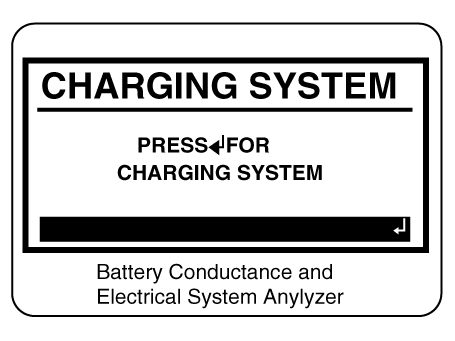
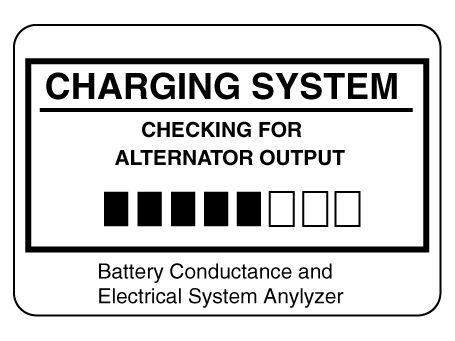
|
12. |
Rev the engine with loads off. (Following the on-screen prompts)
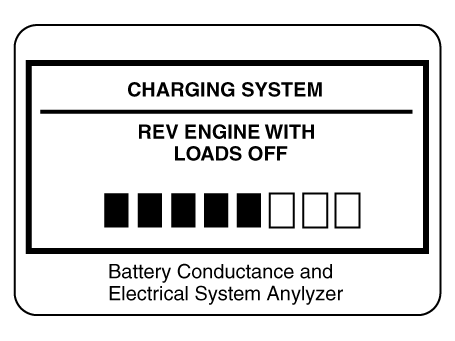
|
13. |
The message that engine RPM is detected will be displayed on the screen,
idle the engine.
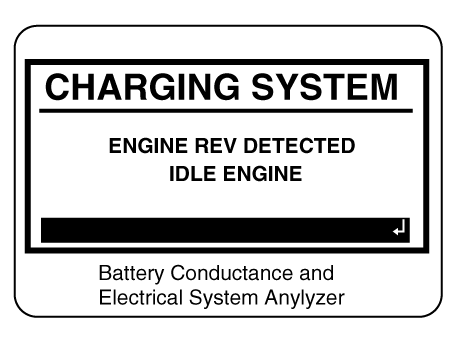
|
14. |
Turn on electrical loads (air conditioner, lamps, audio and etc). Press
ENTER to continue.
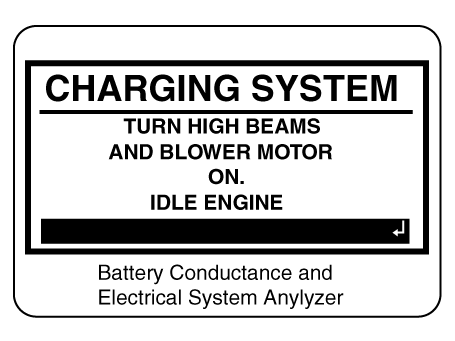
|
15. |
Turn on electrical loads (air conditioner, lamps, audio and etc). Press
ENTER to continue.
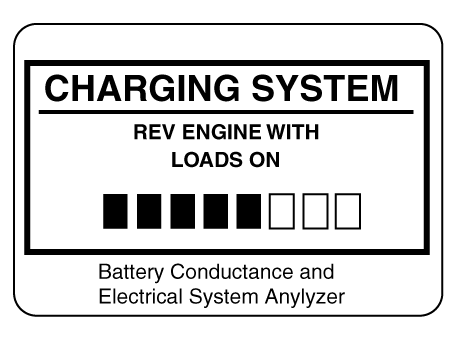
|
16. |
The message that engine RPM is detected will be displayed on the screen,
idle the engine.
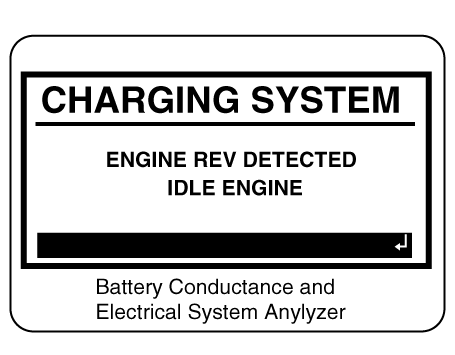
|
17. |
Turn off loads and engine.
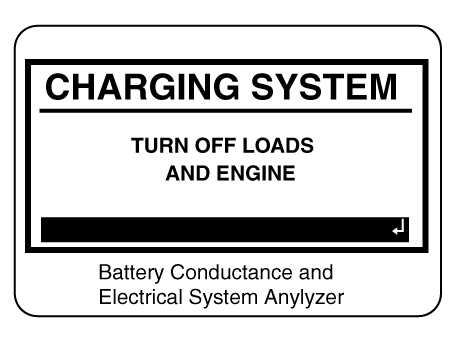
|
18. |
The Charging System decision is displayed at the end of the procedure.
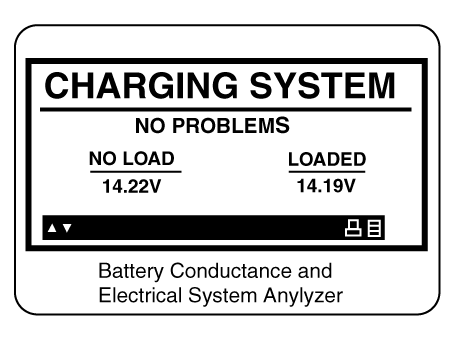
Result On Printer
|
Remedy
|
NO PROBLEMS
|
System is showing normal output from the alternator.
|
NO OUTPUT
|
No alternator output detected.
– |
Check all connections to and from the alternator, especially
the connection to the battery. If the connection is
loose or heavily corroded, clean or replace the cable
and retest.
|
– |
If the belts and connections are in good working condition,
replace the alternator. (Older vehicles use external
voltage regulators, which may require only replacement
of the voltage regulator.)
|
|
LOW OUTPUT
|
Alternator does not supply charging current to battery and electrical
load to system fully.
– |
Check belts and alternator and replace as necessary.
|
|
HIGH OUTPUT
|
The voltage from alternator to battery is higher than normal limit
during voltage regulating.
– |
Check connection and ground and replace regulator as
necessary.
|
– |
Check electrolyte level in the battery.
|
|
EXCESSIVE RIPPLE
|
The voltage from alternator to battery is higher than normal limit
during voltage regulating.
– |
Check alternator mounting and belts and replace as necessary.
|
|
CHARGE BATTERY
|
The starter voltage is low and the battery is discharged. Fully
charge the battery and repeat the starter system test.
|
REPLACE BATTERY
|
Battery must be replaced before the starting system can be tested.
|
|
19. |
Press the BACK/PRINT button to print the test results or MENU to return
to the Options Menu.
|
1. |
Make sure that the ignition switch and all accessories are in the OFF
position.
|
2. |
Disconnect the battery cables (negative first).
|
3. |
Remove the battery from the vehicle.
• |
Care should be taken in the event the battery case is
cracked or leaking, to protect your skin from the electrolyte.
Heavy rubber gloves (not the household type) should
be wore when removing the battery.
|
|
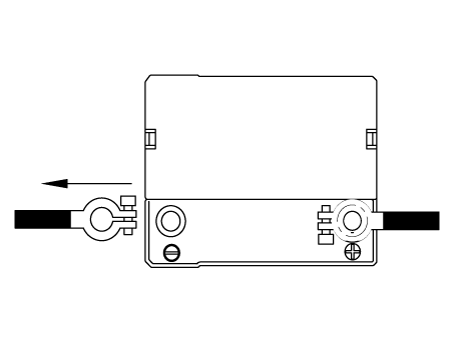
|
4. |
Inspect the battery tray for damage caused by the loss of electrolyte.
If acid damage is present, it will be necessary to clean the area with
a solution of clean warm water and baking soda. Scrub the area with
a stiff brush and wipe off with a cloth moistened with baking soda and
water.
|
5. |
Clean the top of the battery with the same solution as described above.
|
6. |
Inspect the battery case and cover for cracks. If cracks are present,
the battery must be replaced.
|
7. |
Clean the battery posts with a suitable battery post tool.
|
8. |
Clean the inside surface of the terminal clamps with a suitable battery
cleaning tool. Replace damaged or frayed cables and broken terminal
clamps.
|
9. |
Install the battery in the vehicle.
|
10. |
Connect the cable terminals to the battery post, making sure tops of
the terminals are flush with the tops of the posts .
|
11. |
Tighten the terminal nuts securely.
|
12. |
Coat all connections with light mineral grease after tightening.
• |
When batteries are being charged, an explosive gas forms
beneath the cover of each cell. Do not smoke near batteries
being charged or which have recently been charged. Do
not break live circuit at the terminals of batteries
being charged.
A spark will occur when the circuit is broken. Keep
open flames away from battery.
|
|
|
Specification
▷ CMF68L-DIN
Item
Specification
Model type
CMF68L-DIN
Capacity [20HR/5HR] (AH)
68 / 54
Cold Cranking Amperage (A)
600
Reserve Capacity (Min)
110
Specific Gravity
1...
Description
Vehicles have many control units that use more electricity. These units control
their own system based on information from various sensors...
Other information:
Map lamp (LED/Bulb type), Room lamp (LED type)
If the map lamp (LED/Bulb) (1) and the room lamp (LED type) (1) do not operate,
we recommend that the system be checked by an authorized HYUNDAI dealer.
Room lamp, Sunvisor lamp, Glove box lamp and Luggage compartment lamp (Bulb
type)
1...
Inspection
1.
Turn the ignition switch OFF.
2.
Disconnect the intake actuator connector.
3.
Verify that the intake actuator operates to the fresh air position when
connecting 12V to terminal 3 and grounding terminal 7...
Categories
WARNING
To reduce the risk of an air bag deploying unexpectedly and causing serious
injury or death:
Do not hit or allow any objects to impact the locations where air
bags or sensors are installed.
Do not perform maintenance on or around the air bag sensors. If
the location or angle of the sensors is altered, the air bags may deploy when
they should not or may not deploy when they should.
Installing bumper guards with nongenuine Hyundai or non-equivalent
parts may adversely affect the collision and airbag deployment performance.
Press the Engine Start/Stop button to the OFF or ACC position and
wait for 3 minutes when the vehicle is being towed to prevent inadvertent air
bag deployment.
Have all air bag repairs performed by an authorized HYUNDAI dealer.
read more